Quieting air intake in jet engines
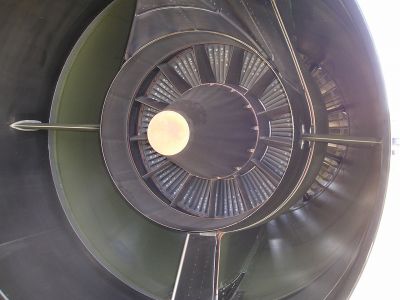
Jet engine turbine
By Dtom (Own work) [Public domain], via Wikimedia Commons
Reducing the acoustic and pollutant emissions associated with air travel has important and broad-sweeping effects for citizens, industries and the environment. A novel acoustic liner for critical aeroengine components will make a major contribution.
Modern turbofan engines, also called bypass engines, have replaced
turbojets in most commercial and military applications while retaining
much of the original architecture. The turbofan sucks in air and
pressurises it as in the past. In contrast to older turbojets, however, a
portion of the compressed air bypasses the combustion chamber and is
ejected out the back to provide additional thrust without fuel
consumption, increasing efficiency.
By enhancing energy efficiency, the fan and bypass system also
facilitate reductions in carbon dioxide emissions. They are also
critical targets when it comes to decreasing noise. Novel acoustic
liners that reduce both weight and noise are on the agenda to meet Clean
Sky Joint Technology Initiative (JTI) requirements. The EU-funded
project 'Large 3-shaft demonstrator - Aeroengine intake acoustic liner
technology development' (ALTD) is playing an important part in this
endeavour.
Scientists plan to bring a promising concept up to a
technology-readiness level of six (TRL 6). This will be achieved with
demonstration of an actual system prototype in an operational
environment, namely an inflight-representative aeroengine ground test.
The intake acoustic liner under development relies on
micro-perforation in which small mechanically drilled holes are placed
in the material to absorb sound, reducing its intensity. Through
extensive data collection and modelling, the acoustic liner and exact
micro-perforation characteristics have been designed and optimised to
satisfy noise reduction targets.
Scientists are also evaluating the materials and effects on the
inner surface of the acoustic liner barrel. Full rain erosion testing
has been completed. Hard particle erosion trials are underway, and
fatigue analyses and effects of ultraviolet light are being considered.
A preliminary design review has led to the ordering of some items
and definition of tooling requirements. The fully configured design is
nearing completion and will be subjected to a critical design review in
the next phase of the mechanical design process.
ALTD's pioneering aeroengine inlet acoustic liner and novel
manufacturing processes will reduce the weight, noise and cost
associated with acoustic attenuation technology. The project will thus
make an important contribution to the EU's Clean Sky JTI for
eco-friendly air transport.
published: 2015-03-09