Novel aircraft composites inspection technology
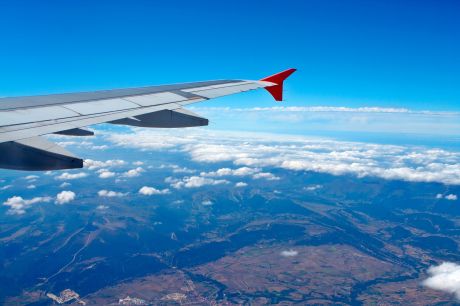
Novel aircraft composites inspection technology
The aerospace industry is actively pursuing research to decrease operating costs while increasing safety and sustainability. Novel non-contact structural health monitoring based on embedded strain-sensitive magnetic wires addresses all issues cost effectively.
With increasing globalisation has come a significant increase in air
traffic over the past decades, and all predictions suggest it will
continue to rise over the next two decades. Improved non-destructive
inspection technologies are critical to competitiveness and
sustainability. They can better detect defects and damage early,
reducing time out for maintenance and costs of repairs. They also
facilitate reductions in the weight associated with incorporation of
additional safety features and thus decrease the load the planes carry
and associated fuel consumption and emissions.
With EU support of the MAGNASENSE (Magnetostrictive sensor applications for self-sensing of composite structures) project, scientists developed smart maintenance technologies for strong and lightweight carbon fibre-reinforced (CFR) composite structures. They are based on strain-sensitive magnetic wires knitted into a metallic mesh and embedded in the CFR composite.
Non-contact magnetic flux sensing arrays scan and map the strain in the composite structures exploiting perhaps the most innovative feature of the system, optical tracking. This is accomplished with an infrared (IR) camera and a transducer with an attached IR light-emitting diode (LED). The LED guides the camera in localising the inspection site. A data acquisition system records the signal and converts it to a numeric format for analysis, all with wireless technologies.
All software and hardware combine to form a sophisticated sensing system for structural health monitoring of CFR composites. Accuracy is enhanced by advanced filtering algorithms. An image correlation tool using the optical metrology compares the structure's surface in reference and test conditions, providing a full-field strain signature. The MAGNASENSE system efficiently indicated areas of potential damage in a test of a component-scale demonstrator, a damaged stiffened panel repaired with a bonded composite patch.
The method provides indications of internal damage quickly, reliably and cost effectively in a non-contact manner. Partners expect to commercialise the MAGNASENSE system very quickly, significantly increasing the global competitiveness of the EU's aerospace industry and the entire supply chain for the product. Widespread uptake will also make an important contribution to the safety and sustainability of flight.
published: 2015-10-23