Electric control of helicopter tail rotors
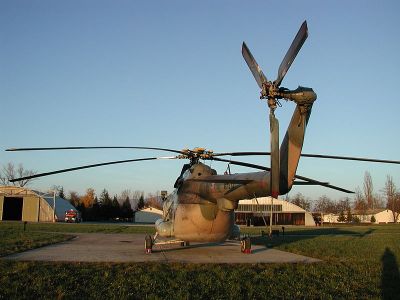
Tail rotor helicopter, fot. Autor Vkinderski (Praca własna) [CC BY-SA 3.0
Most tail rotors on helicopters today are mechanically driven by the main turbine through a mechanical shaft and gears. An innovative electric tail rotor (ETR) promises important environmental benefits as well as improved control and safety.
Mechanical tail rotors work similarly to the way the automobile engine transfers power to the rear wheels of a car. This physical link imposes a fixed relationship between the speed of the main rotor and the tail rotor. It limits the ability of the latter to balance the forces of the main rotor for better manoeuvrability.
An ETR drive would impart independence as well as potentially offer important weight and complexity reductions for enhanced safety and decreased maintenance. The EU-funded project 'Electrical tail drive - Modelling, simulation and rig prototype development' (ELETAD) is examining the feasibility of an ETR drive.
Scientists are adapting ultra-high–efficiency permanent magnet machines currently used in hybrid and electric vehicles to the harsh environment and stringent specifications of a helicopter. This requires the innovative use of advanced materials, intelligent heat management, and intelligent, weight-optimised power control. Objectives include a peak output power of 5 kW per kilogramme of installed active mass and a fault-tolerant design.
The ETR motor software suite consists of modelling tools describing the electromagnetic and thermal behaviour of the ETR motor and assessing the impact of the resultant thermal cycling. It has been released to facilitate trade studies related to various aircraft flight missions. A critical design review of the final ETR motor has now been completed.
ELETAD plans to manufacture and install the ETR prototype motor and test it on an integrated test rig in the coming months. An automated test environment will reproduce realistic tail rotor dynamic loads and the relevant ambient thermal conditions. Importantly, the test rig will include a comprehensive functional representation of a redundant/fault-tolerant electrical supply and control system necessary for safety-critical aircraft application.
Scientists fully expect to deliver a technology demonstrator at technology-readiness level 5, meaning a breadboard technology tested in an environment as close to realistic as possible. Further development and commercialisation will have major environmental benefits, including improved fuel economy, reduced emissions and noise, and minimal use of environmentally hazardous materials such as lubricants. Helicopters are coming of age.
published: 2015-04-21