Tiny holes to boost aircraft efficiency
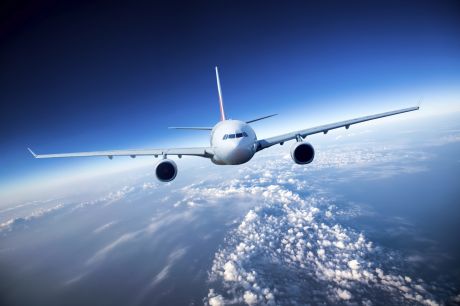
Tiny holes to boost aircraft efficiency
Boundary layer effects play a very important part in determining the drag for an aircraft. EU-funded researchers developed technology for drilling suction holes in the main aircraft drag-producing components, such as the wing leading edges and tailplanes, which promises to bring significant fuel savings.
An effective way of reducing skin friction drag in aircraft is to
maintain a condition called laminar flow in which air slides smoothly
over aircraft surfaces without becoming turbulent. However, small
surface imperfections or disturbances can spoil laminar flow. Many
laboratory experiments and wind tunnel tests have demonstrated that such
a condition can be achieved in another way: suction can delay the
transition of the airflow boundary layer from laminar into turbulent
flow.
Within CLEANSKY-LBD (Adaptation of a generic wind tunnel model for attachment line transition measurements), researchers successfully developed a laser drilling system that produces 400 tiny holes per second of diameter between 50 and 100 μm.
Using a fibre-based high-power laser, the team obtained holes without burrs, which increase unwanted friction and heat. It also overcame challenges related to the drilling strategy and the clamping system, ensuring fast drilling and homogeneous distribution in a two-metre-long panel. The perforated suction skin was integrated into a wind tunnel model with interchangeable inserts.
Skin friction drag accounts for nearly 50 % of the total drag in aircraft. CLEANSKY-LBD technology significantly contributes to the Clean Sky programme's ambitious targets of reducing fuel burn and related carbon dioxide emissions. Successful production of inserts for wind tunnel tests can slash costs and time to market of suction hole technology.
published: 2016-03-23