Generating small vortexes at large aerofoil surfaces
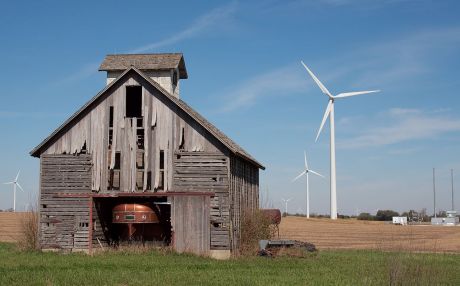
Barn wind turbines
By Dori (Own work) [GFDL (http://www.gnu.org/copyleft/fdl.html), CC-BY-SA-3.0 (http://creativecommons.org/licenses/by-sa/3.0/) or CC BY 2.5 (http://creativecommons.org/licenses/by/2.5)], via Wikimedia Commons
Active control of air flow over large moving structures can significantly improve behaviours in targeted applications. Advanced vortex generators will modify air flow over helicopter or wind turbine blades to increase the efficiency with which they do their jobs.
Adjusting air flow over helicopter blades can decrease drag, reducing
fuel consumption and emissions. In the case of wind turbine blades,
active flow control can significantly increase the efficiency of power
generation.
The EU-funded STA-DY-WI-CO (Static and dynamic piezo-driven streamwise vortex generators for active flow control) project exploited numerical simulation and experimental validation to develop active flow control technology for such applications.
Vortex generators are small devices placed on aerofoils to create swirling motions at the boundary layer (close to the aerofoil surface) to prevent flow separation (when the flow is unable to follow the surface). The team focused on a vortex generator based on a microelectromechanical systems actuator of a piezoelectric membrane. Piezoelectric materials produce a physical displacement in response to an applied electric signal.
Preliminary numerical models facilitated design of two actuators, and the vortex generators were then tested in wind tunnel tests. Experimental outcomes confirmed the potential to reduce flow separation. Given the very light weight and low energy consumption of the piezoelectric actuators, their potential to reduce drag and fuel consumption is very high.
Researchers also conducted acoustic and flutter analysis, the latter related to rapid and irregular motion of the helicopter blades creating dynamic instability. Simulations proved the ability of an acoustic analysis tool to capture near-field sound wave propagation and using it to locate major contributors to noise level. Advanced flutter analysis based on computational fluid dynamics confirmed that ineffective flow control leads to unstable flutter, shortening the lifetime of the blade.
In additional investigations, a rotating machinery test stand was used in conjunction with numerical models to evaluate the structural dynamics of non-linear systems. As a result, the team identified non-linear damping and stiffness characteristics.
All models of subcomponents were integrated on a numerical platform and implemented on a powerful supercomputer.
The STA-DY-WI-CO project has delivered an active flow control technology together with powerful multi-physics simulation code for designers of next-generation aircraft and wind turbine blades. The technologies will reduce fuel consumption, emissions and noise associated with helicopter flight, and increase the efficiency of power generation.
published: 2015-11-02