Strain sensors in aircraft composites
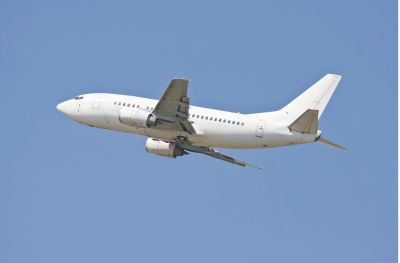
Strain sensors in aircraft composites
Polymer composites have increasingly replaced metal structures in the aerospace industry. Scientists have demonstrated the feasibility of integrating strain sensors for continuous monitoring of structural integrity and major improvements in safety.
Composites offer excellent strength with reduced weight, the latter of
which reduces fuel consumption and emissions. Sandwich structures have
become the preferred choice for light and stiff designs. A thick,
low-density foam forms the core over which thin but stiff skins are
attached.
ROHACELL foam cores produced by EVONIK ROHM GMBH are widely used by the aerospace industry. The cell-structured foams are made from a variety of polymers and the skins or cover layers are commonly carbon fibre-reinforced plastics (CFRPs). The company initiated the EU-funded project SANDWICH FOAM CORES to design and manufacture CFRP sandwich structures with embedded structural health monitoring (SHM) sensors.
SHM is a critical tool to improve the safety and reliability of critical structures. Its integration simultaneously reduces the costs and time associated with maintenance. Small and simple fibre Bragg grating (FBG) sensors are excellent candidates for monitoring the highly stressed CFRPs of aircraft.
FBGs are made from a short segment of optical fibre that transmits specific wavelengths. Strain causes changes in transmitted wavelength, creating a strain sensor. In addition, FBGs are immune to electromagnetic interference, including lightning strikes, and they require no external power. They demonstrate good long-term stability and corrosion resistance, and are well-suited to operation in very low temperatures.
Scientists designed and manufactured novel ROHACELL foam cores. Cured demonstrator parts consisting of stiffened shells filled with foam cores and with integrated FBG sensors were produced in an autoclave. SANDWICH FOAM CORES successfully demonstrated the performance of the FBG sensor in the cured demonstrator parts, confirming the feasibility of integrating SHM systems in composite sandwich structures.
The work will contribute to development of special design rules for such components. Commercialisation of the materials and processes will make a major contribution to the competitiveness of the EU aerospace industry. Enhancing safety, decreasing costs and reducing emissions associated with travel could be a major benefit for other forms of transport as well.
published: 2015-06-26