Innovative heat exchangers for aero engines
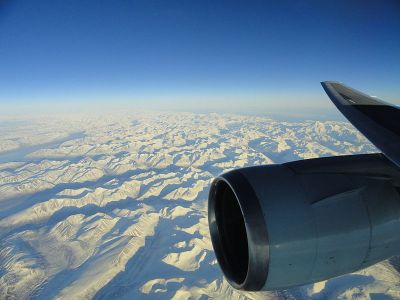
Aircraft engines, fot. By Kristoferb (Own work) [CC BY-SA 3.0
EU-funded scientists are developing advanced surface coolers that are compact and lightweight to cool engine fuel and oil in aircraft. Potential applications include civil markets.
Air-to-oil heat exchangers are an integral feature of advanced turbofan
engine designs. By maintaining oil and fuel temperatures within defined
limits, the surface cooler contributes to achieving optimal engine
performance. The passage of cool bypass flow over the air-washed surface
of the heat exchanger cools oil and fuel.
However, current surface coolers are parasitic to the engine and also occupy surfaces that serve for abating engine noise. As such, their weight, volume and efficiency become critical issues.
In the EU-funded project 'Surface heat exchangers for aero-engines' (SHEFAE), scientists are designing and manufacturing a metallic surface cooler that will replace a part of the core fairing structure. Exploiting existing air-washed structures removes spatial constraints and helps to dissipate more heat. Furthermore, lightweight surface coolers mounted on the fairing result in increased power plant efficiency and reduced fuel consumption.
Use of composite materials for the fairing structure yields additional weight reductions. Research into composite materials, manufacturing techniques and surface cooler structural design includes challenges associated with thermal displacement, sealing and joining.
Once developed, the cooler will be installed and tested on a demonstrator engine, forming part of its heat management system. Project members have drafted the requirements for the structural surface cooler with respect to oil cooling, design point conditions, oil pressure drop and de-congealing. A preliminary and a critical design review are complete. Three newly developed test rigs will validate the component design.
The team has also drafted specifications for the mount composite structure (MCS) and investigated possible geometrical designs that were able to give good specific stiffness at low weight. Focus has been placed on fibre-reinforced composites and their manufacturing for the MCS. The team has conducted experimental tests on composite laminates to identify the main failure mechanisms and validate the newly developed models for composite bolted joints.
SHEFAE is contributing to the highly ambitious goals of the European Vision for Aviation 2050 for serving society and market needs. The project is also strengthening the link between European and Japanese research and technology partners and between European and Japanese industries.
published: 2015-06-09