Safe alternative-fuel vehicles
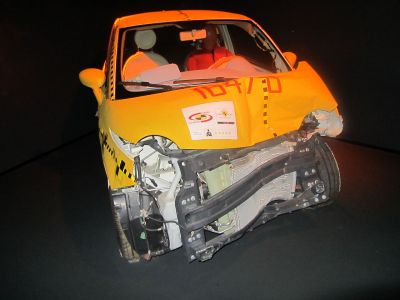
Fiat 500 Crash Test
By Pava (Own work) [CC BY-SA 3.0 it (http://creativecommons.org/licenses/by-sa/3.0/it/deed.en)], via Wikimedia Commons
EU-funded scientists are modelling and testing key composite structures in alternatively powered vehicles (APVs). Investigating the crashworthiness of these lightweight materials is crucial to increasing their widespread commercial uptake.
Currently, the ability to model, simulate and predict the behaviour of fibre-reinforced polymer structures lags way behind compared to pressed-steel car bodies. To address this issue, scientists initiated the EU-funded project MATISSE.
The project is developing and testing modelling techniques for fabric-reinforced structures and thick composites with unidirectional fibres. To validate the modelling approach, focus is placed on designing and testing two important safety-critical parts of future APVs, both being examples of pressurised structures. These are compressed natural gas (CNG) fuel tanks and adaptive crash structures.
By using finite element models, scientists are producing designs for lighter and safer cars with on-board high-pressure storage tanks that are subject to dynamic loading. Work is also geared towards designing and assessing adaptive inflators for pressurising adaptive crash structures. Different pressurisation concepts are explored not only to improve the structure stability in case of crash, but also to provide reduced mass and higher packaging efficiency.
So far, scientists have analysed the most likely crash scenarios to find suitable locations for applying composite structures. A testing methodology for identifying the main load paths on the fuel tank in case of a crash has been defined. CNG vehicles are expected to withstand the forces exerted on the gas cylinder in case of a front, lateral or rear collision, avoiding leakage or fire. Ultimately, making CNG tanks lighter and more tightly integrated into the vehicle not only has environmental benefits, but also increases passenger safety.
Scientists selected a door beam as an application for an adaptive crash structure made of fibre-reinforced composites. Several composite materials have been considered for its design, and the inflating mechanisms have also been produced. Based on these concepts, a prototype beam door has been developed.
MATISSE's ultimate aim is to provide advanced crash modelling tools that should allow automotive designers to adequately simulate and test various safety aspects of APVs. The generated reference designs for adaptive crash structures are also likely to find application in non-APVs.
published: 2015-05-12