Smart miniaturized plastic devices
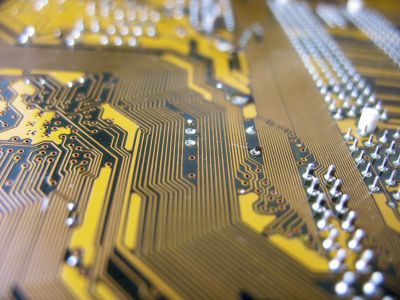
Smart miniaturized plastic devices
Moulded Interconnect Devices (MIDs) combine all the features of moulded plastic parts with electrical circuitry and electronic components assembled directly on the plastic package.
The concept of 3D MIDs has been around since the 1980s. However, although the technology promises major benefits compared to conventional printed circuit boards, a number of issues have proven obstacles to commercialisation. As the technology comes of age, advances could meet the challenges of complex and costly technology requirements.
Annual market growth has been steady at about 20 % for several years and European scientists are planning a strong presence with the EU-funded project 'Pilot factory for 3D high precision MID assemblies' (3D-HIPMAS). Technology will be showcased in a futuristic European pilot factory. Four demonstrators are planned, consisting of micro fuel cells, hearing aids, micro switches and automotive pressure sensors.
Fabrication relies on selective plating processes on plastics based on laser direct structuring (LDS). A laser beam 'draws' a circuit on the surface of a part moulded with a plastic containing a laser-sensitive additive. The surface of the activated plastic is then plated with metal layers similar as used in printed circuited board technology.
Scientists selected plastic raw materials and developed several new high performance thermoplastics containing new fine-grained LDS additives. They also developed a laser machine with a very fine focus and a new plating process for producing finest metal pitches up to 70 µm.
Two-shot moulding, the more established technique, exploits injection moulding of polymer resins in two steps and subsequent activation for conductive metal plating. The innovative experimental two-shot moulding process has been set up as well and the process is being optimised.
Researchers are also developing the required 3D precision electronics components assembly together with reliable monitoring and quality control. 3D assembling and manipulation concepts have been developed for high precision and high throughput. The team is currently putting together the X-ray inspection system that will be used for online process and quality control.
The 3D-HIPMAS technology is expected to reduce raw materials usage, energy consumption and costs, as well as improve cycle time and production yield. A plan is already in place for transfer of building blocks to industrial production plants throughout Europe for increased competitiveness in production of smart plastic micro components.
published: 2015-04-22