X-rays take non-destructive testing in aeronautics to a whole new level
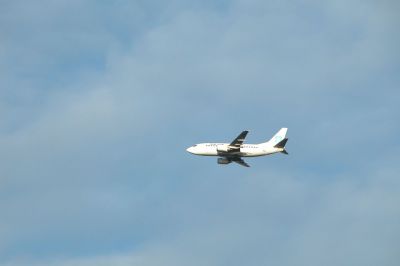
Plane flying to Vágar Airport Faroe Islands
By Erik Christensen, Porkeri (Contact at the Danish Wikipedia) (Private) [GFDL (http://www.gnu.org/copyleft/fdl.html) or CC-BY-SA-3.0 (http://creativecommons.org/licenses/by-sa/3.0/)], via Wikimedia Commons
A novel technology platform exploiting a wide range of X-ray methods (including robot based setups) will facilitate the acquisition of high precision X-ray and X-ray computed tomography (XCT) images of composites. The aerospace industry is thus entering a new era in non-destructive testing of aeronautic components.
Carbon fibre-reinforced polymers or plastics (CFRPs) are lightweight, high-strength materials that have helped the aerospace industry cut fuel consumption and emissions without compromising performance. In fact, the next generation of aircraft, including the Airbus A350 XWB, is targeted to contain more than 50 % of composite materials.
The range of components that can be formed from these materials continues to grow, encompassing designs of complex shape and internal structure. A revolutionary technology platform for non-destructive testing of aeronautic components is currently under development thanks to EU funding of the project 'Quantitative inspection of complex composite aeronautic parts using advanced X-ray techniques' (QUICOM). Much as a medical doctor uses X-ray images for diagnosis, for example, the aeronautic engineers use them to characterize the inner structure of component.
Scientists have developed in this project optimised image acquisition and image processing methodologies capable of analysing the pores, fibre and matrix components of the composites. In addition, simulation scenarios for small, high-volume CFRP parts were generated to represent the individual features as pores, resin, fibres, delamination, etc.
A large variety of CT techniques is under investigation to provide detailed information about the characteristics of the materials and components. These include robot based CT, fast process integrated CT, multi energy CT, high resolution CT, as well as advanced X-ray techniques. For example, single-photon detection has been successfully employed to obtain excellent images of composites with metallic inlays as well as sandwich structures with metal core.
Modelling of large and complex CFRP parts has also been started. A new method to calculate the absolute porosity of composites without using reference samples is currently being developed as well. Finally, two different routes for analysis and visualisation of results are being developed and assessed.
The project web page is up and running and the industrial interest group has had its first meeting. Anyone interested in joining can still do so through the project coordinator. The next industrial interest group meeting is targeted for March 2015.
To sum up, QUICOM's technology platform is expected to revolutionise non-destructive testing of CFRP composites. Cost-effective and rapid access to detailed and non-destructive 3D characterisations will lift the EU aerospace industry to new heights.
published: 2015-04-14