Fatigue testing for composites
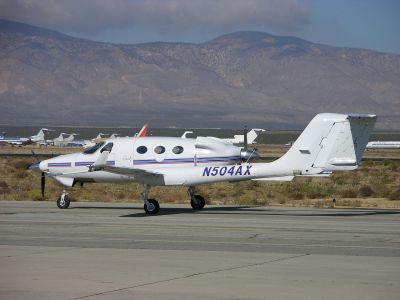
Adam500
By Alan Radecki (Own work) [GFDL (http://www.gnu.org/copyleft/fdl.html), CC-BY-SA-3.0 (http://creativecommons.org/licenses/by-sa/3.0/) or CC BY 2.5 (http://creativecommons.org/licenses/by/2.5)], via Wikimedia Commons
Fibre-reinforced plastics (FRPs) are the building block of numerous aerospace structural components made with stacked configurations. EU-funded scientists have conducted extensive testing and numerical modelling to identify critical failure criteria.
Composites made of a polymeric matrix reinforced with fibres have played
an important role in reducing the environmental impact of numerous
sectors. They reduce the weight of many structural parts and systems
while imparting excellent mechanical properties.
The increasing prevalence of FRPs in safety-critical components
highlights the need for advanced and highly accurate testing and failure
criteria. The EU-funded project MIFACRIT laid the foundations for a
methodology toolbox of accelerated multi-axial fatigue testing with
highly accurate failure criteria. The focus was on one-ply and multi-ply
sandwich or stacked composites for the aerospace industry.
Multi-axial fatigue loading is, as its name implies, loading along
more than one of the three axes of the Cartesian coordinate system.
Until recently, most discussions of cyclic loading assumed uni-axial
loading. However, in real life, many systems such as rotating shafts and
numerous automotive and aircraft components experience a multi-axial
state of cyclic stress.
MIFACRIT addressed this situation for the case of FRPs. Its great
strength lies in the interplay between extensive experimentation and
advanced numerical simulation exploiting methods from fracture and
damage mechanics.
Material tests integrated viscoelastic characterisation during
constant strain and stress tests during cyclic loading. Both temperature
and frequency parameters were varied. The two-stage mathematical
modelling accounts for both local and global descriptions. Simulation
results were compared to experimental ones in a reiterative way to
fine-tune the models. Threshold values for the various criteria were
determined.
MIFACRIT developed the procedure to capture elastic properties and
failure and damage properties of FRPs by evaluating mechanical effects
within the microstructure over various loading conditions. Further
optimisation will enhance the reliability of the assessed properties,
ensuring accurate prediction of the lifetimes of FRPs under multi-axial
load conditions. This in turn will enable more rapid production of
high-quality, safety-critical structural components.
published: 2015-03-16