Development of a Passive Cooling Solution for next-generation aircraft
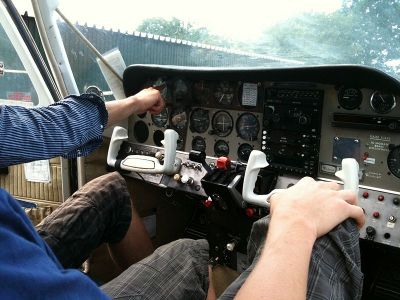
Inside of an airplane, fot. Lars Curfs [CC BY-SA 3.0
More-electric aircraft (MEA) systems feature highly integrated electrical networks in avionics applications. EU-funded scientists are designing a passive cooling system to address thermal management of electrical hardware to guarantee its successful operation and enhance its performances.
Thermal management and reliability of electrical systems in harsh
environments are critical for propelling growth of the MEA market. More
efficient ways of cooling electronic devices using a technique called
heat spreader are becoming a bigger piece of heat transfer solutions.
However, these systems have not been hitherto demonstrated in avionics
applications. Modelling and experimental tests are required before being
integrated in aircraft.
The EU-funded project 'Passive cooling solution validation for
aircraft application' (HTCS) is developing a two-phase heat transfer
system that handles increased thermal dissipation and is passive. The
work will result in a technology-readiness level six of a two-phase
passive cooling system with a high heat exchange coefficient. The
system's maximum temperature is expected to not exceed 200 degrees
Celsius.
Scientists have already established the cooling system
specifications. A trade-off and risk analysis led to selection of a heat
spreader with a body made of nickel, a nickel wick and water as working
fluid. Work is ongoing regarding the establishment of the interface
control drawing, the cooling system design description and
justification, and the breadboarding activities.
Project developments should enable aeronautical actors to completely
switch to a full electrical system with the required reliability even
in extremely constrained environments. The proposed HTCS system will
surpass other cooling technologies in terms of heat management, size and
power density. Furthermore, it will ensure an extended lifetime of the
equipment allowing to reduce maintenability constraints.
published: 2015-03-10