Reducing friction, bearing wear
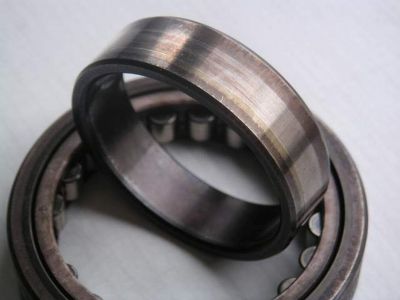
Tarcie
By Jean-Jacques MILAN 00:27, 16 Nov 2004 (UTC) (Own work) [GFDL (http://www.gnu.org/copyleft/fdl.html) or CC-BY-SA-3.0 (http://creativecommons.org/licenses/by-sa/3.0/)], via Wikimedia Commons
Friction between solids in contact arises in a wide range of engineering applications, limiting the lifetime of mechanical systems. As the physical mechanisms governing friction span different spatial and temporal scales, EU-funded scientists developed a multi-scale modelling framework.
Friction and wear caused by the motion of machine components in contact are inevitable. However, there are ways of limiting the amount of friction and extending the lifespan of components and machines while shortening maintenance intervals. Most often, machines are lubricated, and the load is carried by the lubricant as well as asperities.
Lubricants contain additives that chemically bind to metal surfaces to reduce friction. The 'Advanced lubrication modelling' (ALM) project extensively studied the formation of protective layers on components' surfaces when there is insufficient lubricant. Scientists examined whether it was possible to model chemical effects on the nano scale along with mechanical effects on the micro scale.
The Reynolds equations were used to compute pressure distributions over interfaces between machine components in various conditions of lubrication. For thin films, it was important to include the influence of surface roughness (asperities) while solving the governing equations for the pressure. ALM scientists adopted a homogenisation approach to capture the effects of roughness with small characteristic length scales.
Different homogenisation techniques exist, ranging from fairly abstract to those oriented towards industrial applications. The so-called method of multiple scales was sufficiently developed to be used with sets of equations describing two sliding solid surfaces interacting through a thin film of lubricant.
With a deeper understanding of wear on different length and time scales, the ALM scientists then explored the possibility of actively controlling lubricants' flow dynamics. Together with industrial partners, the multi-scale modelling framework was used to reduce the power losses due to friction in a newly designed hydraulic engine.
The versatility of the numerical simulation tools developed within the ALM project has also been proven in the power cylinder design for heavy-duty diesel engines. By reducing the amount of energy lost to heat by friction, its mechanical efficiency was increased with significant implications for fuel and oil consumption.
ALM activities resulted in a comprehensive portfolio of lubrication modelling tools for industry to gain a unique perspective on how to optimise lubrication and achieve results that are both reliable and cost effective. This is expected to become a go-to resource for equipment manufacturers.
published: 2015-02-03