Corrosion protection for more efficient combustion
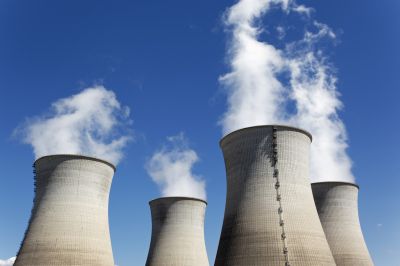
Corrosion protection for more efficient combustion
Much greater efficiencies of coal-fired power plants can be achieved by raising steam turbine temperatures and employing innovative combustion processes. Scientists are developing anti-corrosion coatings to facilitate implementation and fewer emissions.
Reducing both emissions and dependence on fossil fuels is an important
area of energy research. The former is easier to address in the short
term until a transition to renewable energy sources is more cost
effective. Scientists launched the EU-funded project 'Production of
coatings for new efficient and clean coal power plant materials' (POEMA)
to protect materials from the corrosion that becomes more problematic
in high-efficiency scenarios.
The target temperature range is 700 to 750 degrees Celsius. Higher temperatures create steam oxidation and steam-grown oxide scales on the inside of tubing. Fireside corrosion is a synergistic effect among metal alloy materials, flue gas and deposits. It is the leading cause of failure in coal-burning furnaces.
A novel coal-burning process that is the topic of global research could increase the likelihood of corrosion. Oxy-fuel coal combustion, in which coal is burned in an almost pure stream of oxygen, is a more efficient process that uses less fuel. In addition, it produces flue gases consisting mainly of water and carbon dioxide (CO2). The concentrated CO2 stream is easier to purify in carbon capture and sequestration schemes designed to reduce CO2 release into the atmosphere.
Scientists evaluated nano-structured and micro-structured coatings in both air and oxy-fuel combustion. During the first 18 months of the project, work progressed from selection of substrates and coatings for screening, to application and characterisation, to the beginnings of life-cycle assessment.
Metal alloy substrates consisting of a ferritic steel (P92), an austenitic (HR3C) and two alternative nickel-based alloys are being utilised. From the original 31 coatings, scientists have chosen 6 coatings to be optimised for the steam oxidation application and 5 for fireside oxidation protection. To date, all coatings have been applied to the ferritic substrate, and both uncoated and coated samples have been characterised. Lifetime models of some of the coated systems are under development.
Increasing the efficiency of coal-fired power plants will enable significant reductions in CO2 emissions. Corrosion-protection coatings being developed by POEMA scientists promise to enable long-term operation under the required operating conditions with important environmental benefits.
published: 2015-06-02